2022 Look Ahead – Part 2
Posted: January 12th, 2022
Authors: Sheryl W. Paul H. Dustin S. Aditya S.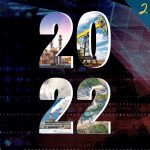
The 2022 Look Ahead is a multi-part series consisting of 20 articles to celebrate ALL4’s 20th anniversary.
Toxics Release Inventory (TRI) – How to Prepare for 2022 Recordkeeping and Reporting // Sheryl Watkins
Since its creation in 1986, toxics release inventory (TRI) reporting has expanded through the addition of chemicals and industry sectors that are subject to the rule. Facilities that are subject to the rule must submit annual reports by July 1 of each year, covering the previous calendar year. Several chemicals have been added to the TRI list for reporting in the past 10 years, including hydrogen sulfide beginning in 2012, ortho-nitrotoluene in 2014, six nonylphenol chemicals in 2015, 1-bromopropane in 2016, hexabromocyclododecane in 2017, nonylphenol ethoxylates category in 2019, and 175 per-and polyfluoroalkyl substances (PFAS) in 2020/2021. To put it in perspective, for calendar year 2019, approximately 23,000 facilities reported to the TRI for total annual releases of all chemicals to the air, water, and land (onsite and offsite annual disposal of waste) of over 30 billion pounds.
There are several additional revisions to the TRI reporting requirements. For example, U.S. EPA is expanding TRI reporting requirements to include the following industry sectors:
- 29 facilities that release and otherwise manage ethylene oxide and ethylene glycol produced using ethylene oxide. U.S. EPA added these 29 facilities because of concerns regarding ethylene oxide’s potential harmful effects on human health, the environment, and potential exposure to workers in facilities that use ethylene oxide. U.S. EPA is also concerned about the toxic effects of ethylene oxide in surrounding communities, including historically underserved communities adjacent to these facilities, and especially the potential for toxic effects in children. In making its determination for these 29 facilities, U.S. EPA considered a variety of ethylene oxide data and believes the 29 facilities selected use the highest amounts of ethylene oxide in the contract sterilization sector and are among those facilities that do not currently report to TRI.
- Natural gas processing facilities. Natural gas processing facilities that primarily recover sulfur from natural gas are already covered by TRI, but this change will expand coverage to include all natural gas processing facilities that receive and refine natural gas. U.S. EPA estimates that at least 321 additional natural gas processing facilities meet the TRI reporting criteria that have not previously reported (i.e., employee threshold of 10 full-time employees or equivalent and the activities threshold, which includes the manufacture, processing, or otherwise use of at least one TRI-listed chemical above applicable threshold quantities). Note: Facilities primarily engaged in natural gas extraction (e.g., exploration, fracking, etc.) are not included.
The facilities mentioned above should begin tracking their chemical activities, releases, and other waste management quantities in January 2022 and, if appropriate, prepare TRI data beginning in 2023. Information collected each year should be evaluated for reporting and documentation, even if reporting thresholds are not triggered.
As noted above, U.S. EPA added certain PFAS to the TRI list of reported chemicals, starting for calendar year 2020 reporting. As part of U.S. EPA’s PFAS Strategic Roadmap released in October 2021, you can expect the following changes regarding PFAS chemicals this Spring that, if promulgated, will be effective for calendar year 2022 reporting (i.e., submit data by July 1, 2023):
- Categorize the PFAS on the TRI list as “Chemicals of Special Concern.”
- Remove the de minimis eligibility from supplier notification requirements for all “Chemicals of Special Concern.”
- Continue to update the list of PFAS subject to TRI, with additional rulemaking expected to add more PFAS to TRI in 2022, as required by the 2020 National Defense Authorization Act (NDAA).
Removal of the current PFAS exemptions and exclusions is expected to enhance the quality and quantity of PFAS information collected through TRI and these changes are expected to expand the number of facilities that will need to report on PFAS chemicals. Two potential implications of this update are that facilities will no longer be able to rely on supplier certifications of de minimis amounts reported in the safety data sheets and facilities will not only need to quantify all applicable PFAS usages, but will also need to identify what specific PFAS compounds are contained in raw materials or products. Stay tuned…
As you know, the TRI has been getting more visibility from the public and more attention from the U.S. EPA in recent years. A higher level of data availability leads to a higher level of data scrutiny. We expect this to continue to be the case, especially with U.S. EPA’s current focus on integrating environmental justice considerations into their plans and actions. For example, the decision to add the 29 facilities in the contract sterilization sector was based in part on the impact of ethylene oxide releases to communities with potential environmental justice concerns. In addition, with continuing enhancements around data gathering, data availability, and integration of data across platforms (e.g., EJSCREEN, a U.S. EPA tool that combines environmental and demographic indicators in maps and reports), the accuracy of the data reported to states and U.S. EPA is of the utmost importance. The TRI website has been overhauled over the years to make it easier for reporters and the public. If you would like to check out the latest data and tools, visit the following link: https://www.epa.gov/toxics-release-inventory-tri-program/tri-data-and-tools.
So, what else can you do to prepare for TRI reporting this year? A few more items are:
- As the TRI requires that facilities use the “best readily available data” in reporting annual releases, and there is more data being gathered and published each year, facilities should evaluate the underlying basis for the data reported to the TRI each year and update, as necessary, to utilize any new site-specific information and any new information published or reviewed by U.S. EPA or by industry-specific technical groups.
- Consider how you can document positive impacts that you have made with respect to pollution prevention as the data submitted through the TRI is also a vehicle to track industry progress in reducing waste generation and moving towards safer waste management alternatives. The TRI serves as a tool for identifying effective environmental practices and a place to highlight pollution prevention successes, especially in source reduction and recycling and to a lesser degree in energy recovery and treatment.
- Compare the reported releases and underlying data for calculations to other facility submittals:
- Annual Air Emissions Inventories;
- Discharge monitoring report (DMR) for releases to water;
- Hazardous Waste Reports;
- Solid waste reports;
- Tier 2 reporting; and
- Any other reports to agencies for 313 chemicals and reports that use production or energy data.
If you need help preparing your TRI or other compliance reports please contact Sheryl Watkins or your ALL4 project manager.
For 2022, U.S. EPA Continues to Focus on NPDES Significant Non-Compliance // Paul Hagerty
The National Pollutant Discharge Elimination System (NPDES), administered by the U.S. EPA, is an enforcement and permitting program which regulates point source and non-point source discharges of pollutants to state and U.S. waters. There are approximately 46,000 individually NPDES-permitted facilities in the U.S. according to U.S. EPA, and it is estimated that of these facilities were in significant noncompliance (SNC) at the beginning of fiscal year (FY) 2018. Although NPDES permit violations can be minor and administrative in nature, such as untimely or inaccurate reporting of monitoring data, it is the SNC violations (e.g., significant exceedances of effluent limits) that have drawn the recent and specific attention of U.S. EPA.
Beginning in FY 2018, U.S. EPA’s National Compliance Initiatives (NCI) have included a goal of reducing by 50 percent the amount of SNC by the end of FY 2022. Why then, in the context of a “2022 Lookahead” article are we talking about an initiative that has been in place since FY 2018? Three reasons – First, U.S. EPA in 2021 elected not to continue other NPDES NCIs (e.g., sewage, stormwater and animal waste), returning them back to the “core enforcement program.” Second, the SNC NCI was modified from the prior cycle and given priority attention. And third, we’re closing in on the end of FY 2022 (September 2022) and the 50 percent reduction has not been achieved yet.
What does this mean for the regulated NPDES community in 2022? Well, if you’re already in SNC, you’re likely already in communication with the regulators to achieve compliance. And if you’re not in SNC, you should strive to remain there. This should include making sure you conduct your monitoring obligations in accordance with the permit conditions and submit accurate and timely discharge monitoring reports (DMRs) so as not to bring attention to your facility. Regardless, based on the increased focus U.S. EPA is putting on NPDES and the NCI, you might want to anticipate additional regulatory scrutiny (e.g., more frequent NPDES site inspections) through FY 2022.
Please contact your ALL4 project manager or Paul Hagerty with questions.
Ambient Air Quality Monitoring Lookahead // Dustin Snare
In 2022, ALL4 expects Federal Reference Method (FRM) and Federal Equivalent Method (FEM) air quality monitoring to remain the standard for supporting air quality decision making, policymaking, and evaluation of attainment status for National Ambient Air Quality Standards (NAAQS) at the state and Federal levels. However, advancements in technology and lower cost instrumentation are aiding the expansion of community-led monitoring networks that are starting to aid in environmental justice efforts. Ambient monitoring networks allow for air quality to be evaluated on a smaller resolution and can help pinpoint local impacts or lead to further studies. As a result of the citizen-science monitoring networks, a tremendous amount of data is being collected.
Community organized low-cost ambient monitoring networks are routinely relying on FRM monitors to be located within the monitoring grid to quality assure the low-cost monitor data and apply correction factors for any data trends analyzed. Ambient monitoring networks can be used in conjunction with local air quality modeling to support air quality forecasting efforts and for predicting pollutant concentrations in the monitoring network region. Ambient monitoring networks could also be used as indicators for where FRM monitoring may need to be sited.
The scientific community is creating measurement instruments for pollutants we didn’t have the capability to measure even a few decades ago (example: Polycyclic Aromatic Hydrocarbons (PAHs)). As measurement capabilities become enhanced, so does the availability of affordable monitoring instrumentation. Citizen-science air quality monitors – monitors that are priced to be purchased by the general public and are widely available with little direction required for setup, use, and data collection – are starting to become a household item and is projected to continue moving that way.
As an example, California enacted a statewide program (Assembly Bill 617) in 2017 to reduce air pollution in communities that are disproportionately impacted by air pollution. The program relies on community partnerships for monitoring air quality. The objectives of Assembly Bill 617 include: better understanding of emissions sources, establishing a baseline of air pollutant concentrations, support development and implementation of emissions reductions strategies, and making the air pollution data accessible to the public. In addition to statewide programs, local and Federal funding is available to enhance ambient air monitoring in communities with health outcome disparities from pollution (environmental justice areas). Just recently the United States Environmental Protection Agency (U.S. EPA) announced a grant competition for a total of $20 million of funding from the American Rescue Plan. Applications for the grants are due in February of this year and are expected to be awarded in the summer of 2022. Community partnerships like the program established in Assembly Bill 617 and agency and local/Federal organization funding for communities such as U.S. EPA’s air quality modeling grants are paving the way for environmental justice area monitoring efforts in the future for not only California, but also the rest of the nation.
ALL4 has experience using the low-cost monitors and can assist facilities in cases where community monitoring is taking place near a facility by reviewing open-source data to understand what the community is seeing. ALL4 has conducted co-located FRM and low-cost monitoring for sites that had small community-led monitoring networks set up around them. We compared the representativeness of the data from the low-cost monitors and background concentrations to site-specific FRM monitor data. If your facility is considering implementing an FRM/FEM monitoring network, consider starting with a low-cost sensor network to assist in determining if FRM/FEM monitoring is worthwhile and/or to assist in the correct site and location for FRM/FEM instrumentation. We can also see ambient monitoring becoming more prevalent to address community concerns about projects facilities are planning to permit and in response to more stringent ambient air quality standards. Please contact Dustin Snare for more information on our ambient monitoring capabilities and to discuss how we can help you with your next project.
Looking Ahead at the Role of Data Analytics in Continuous Monitoring // Aditya Shivkumar
Over the last decade, industries have embraced data-centric approaches in some form to grow and succeed. The data revolution has given rise to a vast number of tools and technologies to help solve complex business and engineering problems. Companies and institutions continue to see benefits of the concept of ‘What is measured, gets improved’ in their decision-making framework. The application of measured data continuously expands especially with the increase emphasis on sustainability and Environmental, Social, and Governance (ESG) objectives.
We see three main factors fueling the growing reliance on data-driven practices within the air quality industry, specifically for entities with continuous monitoring systems (CMS) that already possess a data collection system with large amounts of data. The main factors for the use of CMS data include compliance demonstration and reasonable inquiry, policy making, sustainability reporting, and ESG.
The primary factor is regulatory-driven and relates to the concept of ‘reasonable inquiry.’ Federal and State rules require that the responsible official certify the truth, accuracy, and completeness of the information submitted based upon information and belief formed after “reasonable inquiry.” The responsible official must document that a comprehensive and rigorous program is in place to determine the accuracy of the information reported to the agencies. Outliers, sparse or bad data, and excessive monitoring downtime are some of the key triggers for an agency audit. How do you demonstrate that your facility has systematic processes that fulfill the criteria of ‘reasonable inquiry’? With automated data verification and predictive metrics, owners can effectively show that they have systems in place to check, verify, and confirm the representativeness and quality of their monitored data and as such feel more confident signing the certification of accuracy.
The second reason behind companies becoming more data-savvy is the increasing role of data in policy making. Actual data are very helpful in the current regulatory environment for ground truthing claims about cost and benefit of policy changes. Newer air quality and climate rules have added monitoring and reporting requirements. Data reported by facilities will play a bigger role in the permitting process. To promote transparency and accountability, modern policymaking uses systems that require collecting larger and better data sets to show progress. Clean Air Markets Division (CAMD) is ‘re-engineering’ its data management and reporting systems with enhanced public accessibility and upgrades to allow better integration with other data mapping and reporting tools such as the Power Plants and Neighboring Communities mapping and graphing tools and the Greenhouse Gas Reporting Program (GHGRP).The information reported by facilities is now available to a wider audience using the click of a mouse and this information is only as good as the underlying data collection and verification process.
The third factor is the growing need for companies to demonstrate their efforts toward environmental sustainability or other Environmental, Social, and Governance (ESG) objectives required for consumers, investors, and creditors. In fact, sustainability and ESG will most likely be the primary driver for investment into increased monitoring and data collection in the near future. Typically, monitored emissions and process data are directly fed into sustainability reports. Data-backed key performance indicators (KPIs) and data visualizations can deliver insights and provide an auditable means to track progress against key ESG objectives.
Applications of data analytics in continuous monitoring:
Continuous monitoring systems collect large amount of data. This data can be underutilized and be harnessed to make your static systems dynamic and forward-looking.
Proactive compliance systems: Predicting emissions levels under different operating scenarios will allow facilities to plan ahead and alter their course of action prior to a potential noncompliance situation. Identifying inconsistencies in real-time monitored data serves as an early warning indicator. For instance, consider a power plant that has a regulatory driven requirement to monitor quality-assured emissions data. A faulty component introducing bias in the data can go undetected for days or months, resulting in invalid data, which may lead to penalties for noncompliance. Such situations can be avoided by utilizing process-specific early warning indicators or anomaly detection systems using historical and real-time data.
Equipment reliability: Monitoring systems are complex combinations of components and connections. Equipment fatigue prevents the equipment from functioning at its optimum under set conditions. By applying the principles of reliability engineering and statistics, you can gauge the health of your monitoring equipment, predict equipment problems, and take preemptive action before catastrophic failures. Identifying the deterioration of equipment functionality or performance allows owners to replace/repair the equipment before failure while maximizing its useful lifespan.
Dashboarding and KPIs: Monitored data can be exploited to identify historical trends and establish baseline performance metrics. Combining these metrics into a dashboard will allow personnel to see the compliance status or system performance in one quick glance.
The upside of using data analytics in continuous monitoring:
Owners can realize a high return on investment on utilizing data – or, rather, insights from data – to inform decision making.
Mitigate compliance risk: Identifying compliance risks before they materialize helps prevent noncompliance and associated costs. Auditing your monitoring system periodically against regulatory requirements and building proactive data quality checks ensure the data collected are reliable.
Representativeness and accuracy: Using modern data analysis methods (including the ever-growing application of Artificial Intelligence or AI) to check for inconsistencies, outliers, and suspect data is cost-effective and serves as an additional step in achieving ‘reasonable inquiry.’ Monitored data may be used to justify appropriate permit limits and operational flexibility.
Operational efficiency: Insights from monitored data can also be used to drive process improvements that may lead to cost savings and increased efficiency. For instance, optimizing emissions controls based on real monitored data as opposed to design parameters determined under ideal conditions can reduce operating costs and increase equipment lifespan.
Future proofing and staying ahead of the competition: Companies that adopt data-driven processes are better prepared to thrive in an evolving regulatory environment that is increasingly relying on data for policy changes.
How to get started?
Do not leave the past behind: Start looking at your historical data and monitoring system setup and evaluate them against your regulatory mandates and corporate policies. Conducting third-party audits allow facilities to look at their program through a ‘fresh’ lens and address any vulnerabilities to continually improve the effectiveness of the compliance system.
Understand the present: Tools and technology for turning data into insights have grown exponentially. Can your current system identify issues in real-time (or near real-time)? Are you comfortable with the level of ‘reasonable inquiry’ undertaken to certify your data are accurate? Do you have automated tools to provide quick insights into emissions trends and operating performance? Do you have documentation of processes and procedures for checking the accuracy of your data? If you are unsure about any of these questions, it might be time to evaluate and upgrade your program.
Prepare for the future: Using modern tools and data-driven methods, you can perform ‘What if?’ analyses. Whether it is preparing for stricter regulatory limits, showcasing the impact of your sustainability initiatives or building a next-generation facility using AI, investing in a data centric system will help keep you ahead of the curve.
For more information regarding the benefits of data analytics and how it can support current compliance, operational, sustainability, and ESG initiatives, contact Aditya Shivkumar at 281.201.1239 or ashivkumar@all4inc.com.
What Doug Parker’s Confirmation to Head OSHA Means // Mike Jackson
Doug Parker was confirmed on October 25, 2021, with a 50-41 vote along party lines, by the United States Senate as Assistant Secretary of Labor for Occupational Safety and Health (OSHA). It has been almost five years since the Senate has confirmed a leader for this vital department. Parker takes over for acting OSHA administrator Jim Frederick.
“I’m very excited,” Jordan Barab, the deputy assistant secretary of OSHA for 8 years starting in 2009, had mentioned to news sources. “Doug will be a strong advocate for worker safety and health, and he has the experience and expertise to lead OSHA through these challenging times.”
U.S. Sen. Chuck Schumer (D-NY) was on the house floor the Monday after the nomination and said of Parker “he has a proven track record of protecting everyday Americans in the workplace, which is more important now than ever before.”
Parker had served as head of the California Division of Occupational Safety and Health since September 2019. Before heading Cal/OSHA, Parker was the executive director of Worksafe – a legal services provider in Oakland, CA. Parker held previous roles during the Obama administration as deputy assistant secretary for policy in the Department of Labor’s (DOL) Mine Safety and Health Administration (MSHA) and focused on worker health and safety issues as a member of the current administration’s transition team.
What can we expect from observing Parker’s previous employment with Cal/OSHA?
Doug Parker is expected to lead the federal department the same fashion as Cal/OSHA, with more aggressive enforcement. There will be a greater risk for small businesses under the Biden administration’s “enhanced enforcement efforts” due to an occupational deficiency of expertise, time, and resources that are needed to keep up with intricate OSHA regulations. There are numerous small manufacturing, construction, and industrial companies, with frequent safety hazards classified as major, that struggle to budget for a full-time, competent safety manager.
This lack of resources leaves companies in a continuous state of non-compliance and opens them to failed inspections and huge fines and penalties that the administration has hinted will only increase as more legislation is passed. This strong enforcement precedent should be a warning bell for small business owners and corporations who don’t prioritize safety or have sufficient safety programs in place. Employers should prepare for more aggressive policies by confirming that their safety and health programs are compliant with rules that, while not historically enforced, are still in place and regulate American facilities.
If we look to Cal/OSHA as a blueprint for Parker’s priorities, items that may be prioritized include California’s Injury and Illness Prevention Program (IIPP), ergonomics standards to address repetitive motion injuries, and workplace violence prevention in healthcare.
Health and safety issues are at the forefront of policy making, and companies need to be aware of how this could affect their business operations moving forward. Do you have questions about OSHA or general Occupational Health and Safety? Please reach out to Sheryl Watkins at swatkins@all4inc.com.