The Dos and Don’ts of Meteorological Monitoring
Posted: May 9th, 2016
Authors: Amanda E.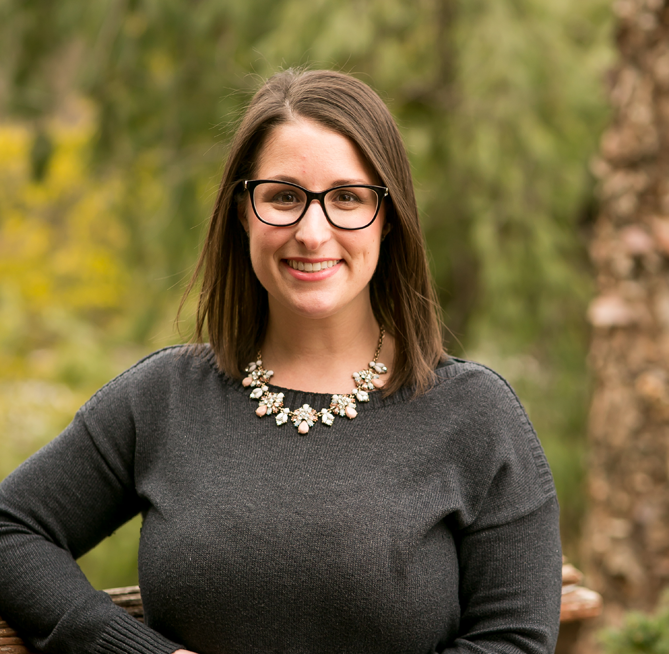
One of the service areas ALL4 provides our clients is the setup, maintenance, and breakdown of meteorological monitoring towers. For some, on-site meteorological data are required for air dispersion modeling demonstrations; for others, meteorological monitoring data are required as part of a regulation (e.g., the Refinery Sector Rule’s benzene fenceline monitoring requirement). Whatever the reason, ALL4 has helped numerous clients with the task of setting up and maintaining a meteorological tower equipped with the associated instruments. In a blog I posted in June 2015, I wrote about some of my experiences out in the field, and some of the regulatory background as to why I was out there. This follow-up blog will dig deeper, and divulge some of ALL4’s secrets to success by exploring the “Dos and Don’ts” of meteorological monitoring. We had to learn some of these points the hard way, but we are a better team because of those experiences!
DO: TEST EQUIPMENT AT THE OFFICE
DON’T: ASSUME IT WILL ALL WORK ON SITE
When ALL4 orders meteorological equipment, we always have it delivered to our office well before the installation is scheduled. Prior to bringing it to the project site, we test the datalogger, program, and wiring to ensure that everything was set up correctly. We make sure that we can connect to the station with our laptops. Before our audits of existing installations, we test the audit equipment connections and readings to mitigate possible issues we could have out in the field. Sometimes, even with this preparation, meteorological sensors can break once they are deployed. For example, about two (2) weeks after we installed a tower, one (1) of the sensors started reading “0”. ALL4 had to arrange a trip out to the tower, replace the sensor, and send the sensor back to the manufacturer. We found out later that the circuit board of the brand new sensor needed to be replaced. What are the odds?
DO: UTILIZE AN EQUIPMENT CHECKLIST
DON’T: ASSUME THAT EVERYTHING IS IN THE BOX
This is a biggie. Before every trip, whether it is a tower installation or audit, we print out our checklist and go through it – multiple times. We assemble the equipment the day before the trip, and then go through the checklist again the day of the trip. Even if you ‘know’ that equipment should be in a box, we always pull out each piece to verify that we are bringing what we need. Sometimes, during this process, we will identify equipment or tools that are missing, and we will take a trip to the local hardware store to pick it up. Last year, while at a site for a meteorological tower audit, our ratcheting wrench set was unable to loosen an old (and I mean old), rusty bolt to let down the tower. We didn’t have a simple, adjustable wrench with us, which would have saved a good bit of time. We ended up using – and I kid you not – a bottle opener to loosen the bolt! Now, we have an adjustable wrench in the ALL4 toolbox, and I store an adjustable wrench in my car (a Christmas gift from my dad last year).
DO: BE SAFE
DON’T: TAKE ANY CHANCES
As with any of ALL4’s site visits, we not only comply with the site’s safety rules, but with ALL4’s safety policy as well. When you see us out in the field, we’ll at least be wearing long pants, steel-toe/composite toe boots, safety glasses, and a sweet ALL4 hard hat. You never know what hazard you will run into (literally – 2-meter boom arms are just low enough to cause head bumping issues)! In my blog last year, I told you about being out in the polar vortex; we had to make sure we were prepared for the below 0°F temperatures. In the summer, our main adversaries are bees and wasps; they really love the aluminum tower and we often find them nesting in and around our enclosures, so we bring wasp spray with us to battle them. Some other useful weapons to have in your arsenal include bug spray, sun screen, water, and snacks. Let me remind you that these jobs are outside and usually in remote areas so that there is minimal disturbance of the data. Due to the remote location, we are usually on the site for extended periods of time without the option of stopping over at a nearby convenience store for a coffee or a protein bar (let alone lunch!). Snacks need to be pre-planned and packed ahead of time. There is nothing worse than fighting the battle against your stomach while you are trying to perform intricate tests with delicate equipment. Not to mention that at some of our more remote sites, we have been in earshot of gunshots and had visits from nosy, rifle-carrying, ATV-driving locals.
DO: BRING SPARE EQUIPMENT
DON’T: ASSUME “WE’LL BE FINE”
When ALL4 is responsible for ordering and installing a meteorological tower, we always order spare sensors to keep on site just in case there is a problem. During audits, we rely on these onsite spares, or, if it is a remote site, we bring spare sensors with us, just in case nature damaged our sensors (such as a large bird) or a person on the project team gets their steel-toe safety boots too close to the equipment. Of course, the one (1) time we didn’t bring a spare, we ran into a problem with a plastic cupset… but don’t worry – the team member’s toes were properly protected with the steel -toe barrier (we are always on top of our safety policy). One (1) of the cups snapped off, and we were five (5) hours away from the office. An awesome ALL4 employee (shout out to Kayla!) drove out and met us halfway to give us the replacement parts that we needed to finish the job that day – even if it meant putting in a few extra hours. Needless to say, we always carry spares of everything for these trips!
DO: CHECK ON THE DATA DAILY
DON’T: CHECK ON THE DATA AT THE END OF THE QUARTER
As part of ALL4’s maintenance of meteorological towers, we download and review the data daily. We have a dedicated computer that remotely connects and downloads data from each of the sites we maintain. Then, a technical staff member reviews the data to confirm that the sensors appear to be working properly. If the meteorological tower is being used to provide data for air dispersion modeling, U.S. EPA requires at least 90% of each calendar quarter to have complete data. If you are only checking on your data at the end of the quarter, an extended period of downtime might lead to an issue with meeting that requirement. This issue can be avoided if someone is routinely checking the data so that valuable time is not lost if a trip needs to be planned to replace a faulty sensor. In the example above, the only way we found out that the sensor wasn’t operating correctly (since the circuit board had broken) as by performing daily reviews of the data.
Working with meteorological towers and the data they collect are one (1) of my responsibilities at ALL4. I like going out into the field (love the change of scenery) and getting to work with my hands. If I have learned anything from these trips, it is that A LOT of time and planning goes into each of these visits (that includes late nights and long drives). It is crucial to be prepared and to take all of the precautions that you can to ensure that you will have a safe, efficient, and successful trip in the field. Main take-away: Always expect the unexpected.
Want to know more? Shoot me an email at aessner@all4inc.com, or reach out to our Technical Manager, Dan Dix at ddix@all4inc.com!