Oxygen – We need it to live, and so does your 40 CFR Part 63, Subpart DDDDD Boiler!
Posted: December 16th, 2015
Authors: Susie B.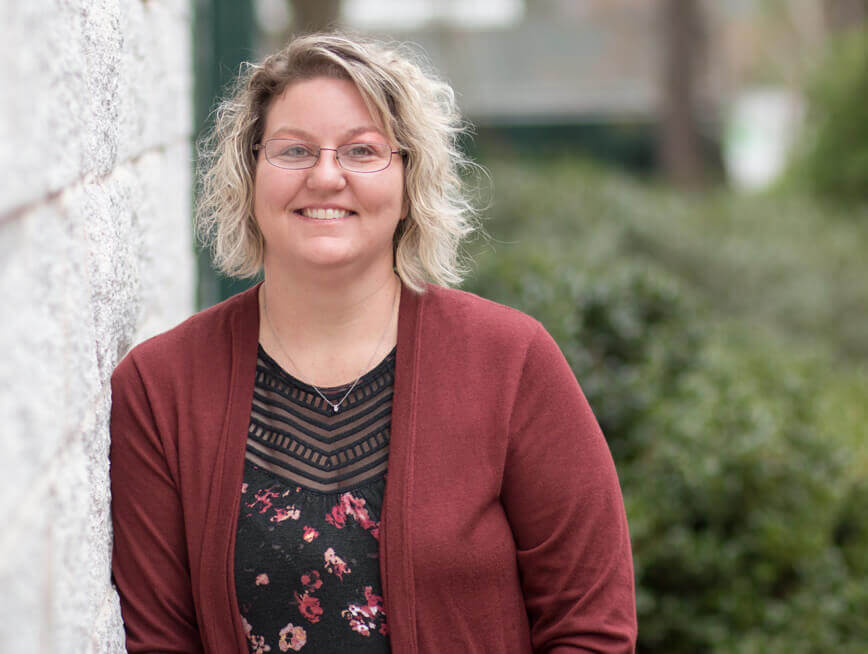
Let’s talk about oxygen! Sure, we all know that it’s critical to life, but did you know that it is also a critical part of the major source Boiler MACT1 rule? According to 40 CFR §63.7525(a), a boiler or process heater that is subject to a carbon monoxide (CO) emissions limit must install, operate, and maintain an oxygen (O2) analyzer system, or install, certify, operate, and maintain a continuous emission monitoring system (CEMS) for CO and O2. Have you determined how you will demonstrate continuous compliance with the requirement to monitor O2? There are multiple ways to meet this requirement. The following may be utilized:
- Boiler O2 (for boilers without an O2 trim system)
- O2 trim system
- O2 measured at the stack through an existing analyzer
Let’s take a closer look at the options.
For boilers without an O2 trim system, an O2 monitor must be used to measure and record the O2 content in the boiler or process heater flue gas, boiler or process heater, firebox, or other appropriate location.. The data from this monitor would be reduced to 30-day rolling averages. The 30-day rolling average would have to be maintained at or above the lowest hourly average measured during the most recent CO performance test.
One of the least burdensome methods is utilizing an O2 trim system. Pursuant to 40 CFR §63.7525(a)(7), a facility would operate an O2 trim system at the O2 level set no lower than the lowest hourly average O2 concentration measured during the most recent CO performance test. This minimum O2 concentration is then established as the set point for the O2 trim system. The facility must continuously operate the boiler at or above this set point. If a facility chooses to comply with this option, then O2 content is not required to be monitored on a 30-day rolling average. The facility must monitor the O2 trim set point and whether the O2 trim controller is in automatic or manual mode of operation.
For boilers that operate a CO CEMS to comply with the alternative CO CEMS emissions standard, the O2 operating limit does not apply. Another option may be to use an existing CEMS that measures O2 for another requirement, such as an existing nitrogen oxides (NOX) CEMs that is being used for compliance with 40 CFR Part 60, Subpart Db. Based upon U.S. EPA guidance, a facility can use O2 measurements from an existing CEMS in the stack to satisfy the O2 monitoring requirement. U.S. EPA also advised that the wording “at the outlet of the boiler” in 40 CFR §63.7525(a)(1) would include the stack. Similar to the option mentioned above, the facility would continuously monitor O2 content from the CEMS and reduce the data to 30-day rolling averages. The 30-day rolling average would have to be maintained at or above the lowest hourly average measured during the most recent CO performance test.
No matter which option is chosen, the O2 monitoring procedures must be documented in the site specific monitoring plan (SSMP). The SSMP must be prepared according to the requirements in 40 CFR §63.7505(d)(1) through (4). For O2 monitoring, the SSMP must include installation and ongoing quality assurance requirements.
If you have questions regarding your O2 option, feel free to give me a call at (334) 855-3382 or reach out to me via email at sbowden@all4inc.com.
1 40 CFR Part 63, Subpart DDDDD (National Emissions Standards for Hazardous Air Pollutants for Major Sources: Industrial, Commercial, and Institutional Boilers and Process Heaters) establishes Maximum Achievable Control Technology (MACT) standards for boilers and process heaters at major sources of hazardous air pollutants (HAPs).
For more information about Boiler MACT, please visit our 4 Rules (Boiler MACT) Initiative page.