Life Cycle Assessment of Lithium Ion Batteries
Posted: September 28th, 2023
Authors: Daniel H. Louise S.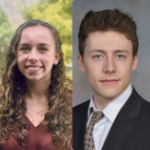
Life Cycle Assessment (LCA) is a systematic tool used to assess the environmental impact of a product, process, or service throughout its entire life cycle. LCA looks at the entire life of a product or process, from extraction of raw materials to product disposal, and allows businesses to identify materials and processes within a product’s life cycle that pose the greatest environmental, occupational, and public toxicity impacts.
The impact of climate change is becoming of increasing concern to many countries. Companies and governments alike are trying to move away from fossil fuels and electrify the economy, which makes electricity storage very important, specifically with lithium-ion batteries. Lithium-ion batteries produce a rechargeable form of energy used in many electronic devices such as cell phones, laptops and solar back up storage. However, the recent surge in demand for lithium-ion batteries has been accompanied by growing concerns over the environmental impact of the materials found within these batteries, such as lithium, cobalt, and nickel.
How do Lithium-Ion Batteries Impact the Environment?
The life cycle of a lithium-ion battery begins with the extraction of raw materials from sites such as lithium and cobalt mines, where practices like open-pit mining and brine extraction mining are used. These mining practices cause hazardous materials to enter ground and surface water systems, where they have been demonstrated to cause drinking water contamination and ecosystem degradation. These practices have also been connected to the overconsumption of water, using nearly two million liters of water to extract a single ton of lithium.
Once the raw materials are obtained, they undergo processing to create the active components of the battery, such as cathodes, anodes, and electrolytes. These components are then assembled into cells, and multiple cells are combined to form a battery pack. Processing operations such as material refining and smelting are very energy intensive and result in air emissions from operating machinery at high temperatures. Once a lithium-ion battery completes all manufacturing and processing steps, it then is used in commercial products for its useful lifetime.
Once lithium-ion batteries are used in commercial products the electrical energy consumed during the usage and recharging cycles can contribute to greenhouse gas emissions and other environmental impacts, depending on how the electricity is sourced (renewable vs non-renewable sources). Recharging lithium-ion batteries with electricity generated from a coal power plant or another non-renewable energy source can only be made possible from combustion reactions that release greenhouse gases and other pollutants, such as carbon dioxide (CO2). For example, a full charge for the battery found in a 2022 Tesla Model X warrants approximately 115 kilowatt-hour (kWh) of electrical power, which can result in an estimated 98 pounds (44.45 kilograms) of CO2 emissions from a coal-fired power plant. The wide variation in use and sizes of lithium-ion batteries makes it difficult to accurately quantify the environmental impacts.
How are Lithium-Ion Batteries Disposed of?
Upon reaching the end of its useful life, a lithium-ion battery is intended to be disposed of at designated recycling locations or household waste collection sites. When this occurs, the materials within lithium-ion batteries may be recovered and recycled for future use, or the entire consumer product may undergo refurbishing to render the product useful once again. There are currently three different methods for lithium-ion battery recycling which are hydrometallurgical recycling, pyrometallurgical recycling, and combination of both metallurgical techniques. Pyrometallurgy is where the cathode and anode materials are recovered through smelting. Hydrometallurgy is where the electrolyte solution is evaporated and condensed to recover the lithium salt electrolyte solution for reuse. A combination of both processes can increase recovery efficiency. Although these recycling activities can reclaim and recover significant amounts of material for reuse, they also generate large quantities of air emissions and contaminated water. Out of these methods, pyrometallurgical recycling has the highest overall environmental impact, especially in the eutrophication potential and abiotic resource depletion potential. Hydrometallurgy has a comparable environmental impact to the combined metallurgical techniques depending on the leaching agent used for hydrometallurgy. Overall hydrometallurgy does not use much energy which leads to a lower global warming potential while it does have harmful effects depending on the leaching agent used.
Unfortunately, it is estimated that only five percent of lithium-ion batteries are properly disposed of at designated recycling facilities, and that the remaining ninety-five percent are improperly thrown away or recycled in at-home waste or recycling bins, resulting in most of these batteries ending up in landfills, oftentimes starting chemical fires during transport. When this occurs, the contents of these batteries can leach into the soil and water table, endangering the health of the local ecosystem and any nearby residencies.
How Do Recycled Batteries Make a Difference?
Proper recycling of lithium-ion batteries conserves resources and reduces the environmental impact of resource extraction and minimizes the disposal of hazardous waste. Generally, lithium-ion batteries are considered highly recyclable, with a significant portion of their components being recoverable and reusable. For instance, nearly half of the copper in discarded lithium-ion batteries can be recovered through recycling processes and reused in the production of new batteries.
Likewise, advances in recycling methodology have allowed for increased yields of recovered materials from spent lithium-ion batteries. Techniques in electrolyte recovery and treatment, such as alkaline absorption, pyrolysis, and solvent extraction have bolstered recovery efficiencies to nearly 87% and have recovered lithium in the form of lithium carbonate (LiCO2) at levels as pure as 92%. These levels of material recovery allow for recycling facilities to treat spent lithium-ion batteries like highly enriched ore.
Additionally, it has been found that cathodes made from recycled materials allow for better performance and a longer lifetime from a lithium-ion battery than virgin materials do. A study conducted by Worcester Polytechnic, Rice University and Argonne National Laboratory found that lithium-ion batteries that had been fitted with recycled LiNi1/3Mn1/3Co1/3O2 cathodes degraded at a much slower rate, providing 11,600 battery discharge-recharge cycles before degrading to a capacity retention of 70%. This represents a performance increase of 52.6% when compared to the control group of virgin LiNi1/3Mn1/3Co1/3O2 cathodes, which provided 7,600 discharge-recharge cycles before degrading to the same capacity retention.
How Can LCA Benefit My Facility?
Although LCA isn’t a practice that is mandated by any state environmental authorities or by the United States Environmental Protection Agency (U.S. EPA), doing so can identify improvements within a product’s life cycle, and allow a business to meet desired environmental, social, and governance (ESG) metrics by making more environmentally conscious decisions when sourcing, processing, or disposing of hazardous waste. However, most lithium-ion batteries are likely to meet the definition of hazardous waste under the Resource Conservation and Recovery Act (RCRA). Therefore, the U.S. EPA recommends that businesses consider managing lithium-ion batteries under the federal regulations for ‘universal waste’, as defined in Title 40 of the Code of Federal Regulations (CFR) Part 273.
If you are interested in conducting LCA on any processes or products generated at your facility, please contact Louise Shaffer at lshaffer@all4inc.com for more information. Likewise, if you have questions or concerns regarding the hazardous waste generated or being disposed of at your facility, please contact your ALL4 Project Manager or Daniel Hickey at dhickey@all4inc.com for assistance in meeting state and federal environmental compliance.