Why are Safety Data Sheets Important in the Workplace?
Posted: August 31st, 2023
Authors: Noel A.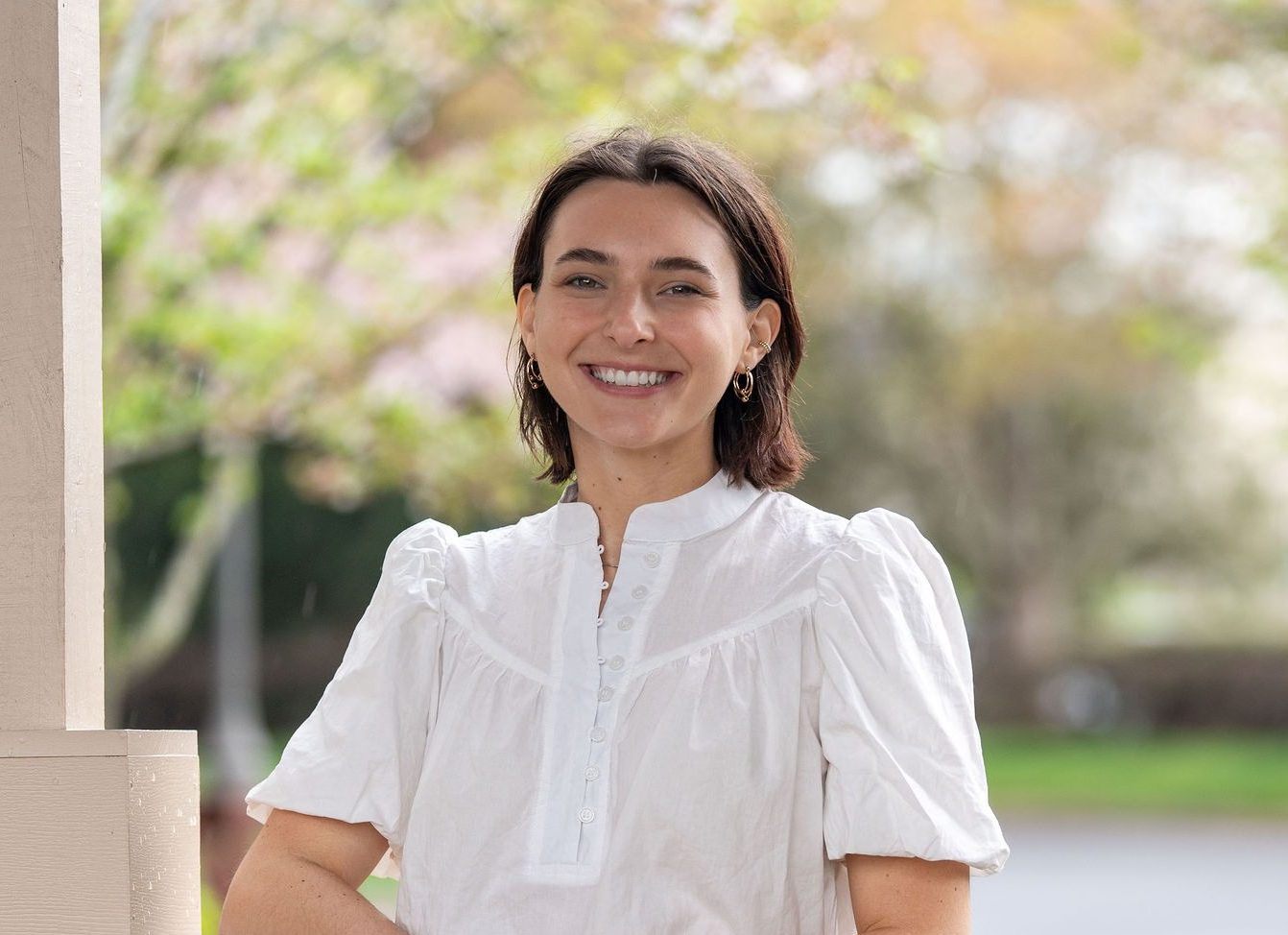
What are Safety Data Sheets? The health and safety of all employees is essential to providing the best services to clients. Reduction in chemical source illness and injuries in the workplace allow employers and employees to work safely with chemical materials. In order to maintain this standard, the Occupational Safety and Health Administration (OSHA) constructed the Hazard Communication Standard, which ensures that all employees keep their staff safe through communicating chemical information with Safety Data Sheets (SDS). In 2012, OSHA made major changes to the Hazard Communication Standard to standardize the criteria for classification of hazards and provide labels for the chemicals to be consistent and easier to understand. These changes align with the GHS (Globally Harmonized System of Classification and Labeling of Chemicals). The GHS is a living document that provides an internationally negotiated approach to labelling and formatting hazardous chemicals. The change also involved revising the name from Material Safety Data Sheet (MSDS) to SDS.
This is the first in a series of 4 The Record (4TR) articles that will provide you with how and when to use your SDS in other regulatory programs such as TRI reporting, Air Emissions Calculations, release reporting, and waste determinations to name a few.
SDS include information on the properties of chemicals and their safety measures that should be followed by the chemical manufacturer, distributor, or importer and to the consequent user. SDS are created by the manufacturer or distributor of hazardous chemicals. They include 16 sections which include listing properties, hazards, safety precautions for storing and protective measures for handling the chemical. The standardized information contained in SDSs makes it easy and effective for providing information on chemicals.
- How can I find information in the Safety Data Sheet? SDSs have 16 sections that contain information such as:
- The properties of each chemical
- The physical, health, and environmental health hazards associated with the chemical
- Protective measures
- Safety precautions for handling, storing, and transporting the chemical
Sections 1 through 8 contain general information about the chemical, identification, hazards, composition, safe handling practices, and emergency control measures (e.g., firefighting). The first aid and accidental release measures described in these sections are helpful in case of exposure to chemicals. This information should be helpful to those that need to get the information quickly. Sections 9 through 11 and 16 contain other technical and scientific information, such as physical and chemical properties, stability and reactivity information, disposal practices, toxicological information, exposure control information, and other information including the date of preparation or last revision. It should be noted that SDSs are only required for hazardous chemicals, but many customers require SDSs on all products, whether they are hazardous or not. OSHA does not require or encourage this practice; they can’t prohibit producers from distributing nonhazardous SDSs. Items that are not hazardous or are exempted are listed in the OSHA HazCom Standard 29 CFR 1910.1200.
- How does this apply to employers and their employees? The HCS requires employers to keep an updated Safety Data Sheet for every hazardous chemical used or stored in the facility, regardless of the frequency or amount of chemical used. Facilities where hazardous chemicals are handled are required by law to either retain hard copies of SDS or teach all employees how to obtain SDS electronically. Administrators can request additional copies of SDSs from chemical manufacturers at any time. Employers must ensure that the SDSs are readily accessible to employees for all hazardous chemicals in their workplace. Employees must be trained in the physical and health hazards of the chemicals in the workplace, the recommended measures to use products safely, and recommended emergency procedures for cleaning up a spill or release of chemicals.
- How do I keep up with revisions being made to SDS? The GHS is updated every biennium to improve alignment and effectiveness of SDSs. Referring to revision 7, OSHA is proposing changes to the HCS to improve the comprehensibility and utility of the standard and allow the HCS to keep up with new technologies to better protect workers’ health and safety. It is unknown when the proposed rulemaking will be voted on by Congress, but the Final Rule was originally supposed to be issued in June of 2023.
ALL4 is here to answer your questions and assist your facility with keeping up with regulatory changes. All4 offers numerous OSHA Compliance services within the environmental, health and safety consultation field. Identifying and reducing hazards in the workplace for your facility can be challenging, and All4 is able to interpret and evaluate the correct strategy to achieve regulatory compliance, reduce risk and provide a safe and healthy workplace. If you have any questions or would like to speak to one of our Health and Safety Practitioners, please contact Noel Attwood at nattwood@all4inc.com or Kevin Chaplin at kchaplin@all4inc.com.