Time to Upgrade Your Facility’s Data Management System?
Posted: December 2nd, 2015
Authors: Eric S.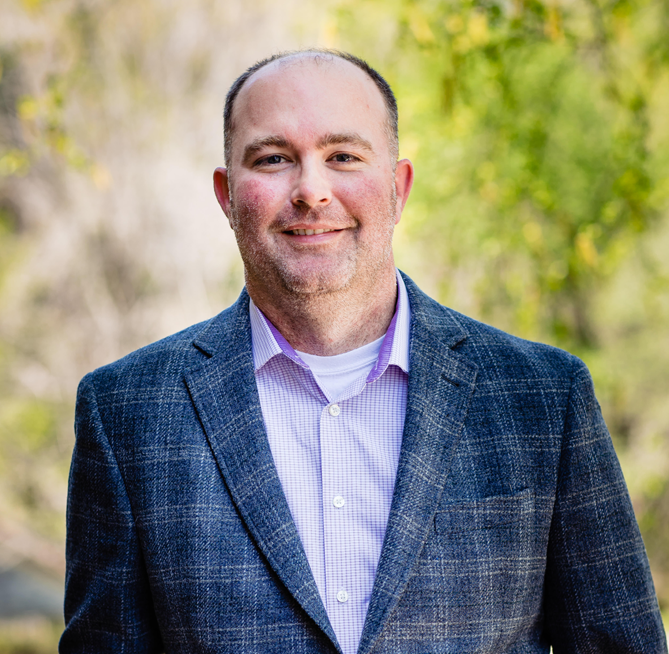
”
Are you worried about your compliance approach using data collected from continuous monitoring systems (CMS) at your facility? Or maybe the inefficiencies in your process you currently use for managing your data cause you to periodically lose sleep. It is only a matter of time before someone (i.e., a regulator) starts asking questions about your CMS data whether it is in response to reports submitted to regulatory agencies or as part of an internal or third-party audit. One (1) solution is to get that data under control and to fully understand how compliance with your emissions limits is demonstrated by your CMS. Maybe it is time to install a new, or upgrade an existing, data acquisition system (DAS) to manage measured data from CMS at your facility. A DAS manages your CMS compliance data from collection, validation, and calculation, through notification, recordkeeping, and reporting. To get the most out of a DAS, your (and your facility’s) involvement needs to go far beyond the selection of the DAS software or vendor. It requires the dedication of resources to properly implement and integrate the DAS into your facility’s compliance solution. A properly selected, integrated, and implemented DAS can make you wonder how you ever got by without a DAS (or if upgrading an existing DAS, how you ever were able to confidently assess your facility’s compliance status with the previous DAS). One (1) of the most important roles of a DAS is to serve as a tool to enable you to assess your facility’s compliance status with the various environmental regulations where compliance is demonstrated using a CMS. Another important role of the DAS is to generate reports from a database containing CMS data that can withstand scrutiny from regulatory agencies, internal or third-party auditors, environmental groups, or anyone else that may be accessing and reviewing your data in the public domain.
So you have come to the sobering conclusion that there is now way too much CMS data collected at your facility to handle with your current system and you will not be able to survive without a new or upgraded DAS. Why not implement a DAS that integrates into your existing systems and provides an increased efficiency for managing your compliance data? Outside of the data management piece, one (1) of the most important aspects of a DAS is that it provides a platform for delegation and accountability. In a typical facility structure, the Instrumentation, Operation, and Environmental Departments all serve important roles in the generation and utilization of CMS data for compliance demonstrations. The Instrumentation Department is responsible for providing quality-assured data from the CMS and minimizing CMS downtime. The Operation Department is responsible for considering CMS data while operating sources within regulatory parameters and implementing corrective actions when a regulatory parameter is exceeded. The Environmental Department is responsible for overseeing the systems, including the DAS, used by the Instrumentation and Operation Department to fulfill their responsibilities. A DAS that is fully implemented should provide the means for the Environmental Department to delegate the responsibility of CMS downtime to the Instrumentation Departments and the deviations or excess emissions to the Operation Departments.
Because the Environmental Department typically is responsible for supplying the tools needed for the Instrumentation and Operation Departments to do their jobs, it is important that the DAS is fully implemented and integrated into the facility’s existing system. Let’s ask ourselves several questions to better understand how to pull all of the pieces together to provide a compliance solution that gives you, the Environmental Manager, confidence and makes the job of the Environmental Department clearly defined and more efficient.
How do you manage your CMS compliance data now?
Let’s start with an honest assessment of your current DAS (or lack thereof) and data management systems to highlight inefficiencies (and possible regulatory exposures). Are there aspects of the management of your compliance data keeping you up at night? Or maybe you have inherited a legacy system and you just do not know how it works. Could you explain to a third party or the person certifying compliance at your facility how compliance averages are built? If you have a DAS, request a specification from the vendor that summarizes how the data are validated, expressed in terms of the emissions standard, and averaged for purposes of demonstrating compliance. If you have an in-house data management solution, find “that person” at your facility who can tell you how the data are handled. Questions to be thinking about are: how are invalid data (e.g., in calibration, in maintenance, out-of-control, etc.) handled; how data collected when the unit is offline are considered when building compliance averages; how are compliance averages built and validated. Let us not forget the regulatory references for the basis by which the data management process was selected. You might be surprised what you find out about your data management system and what it is (and isn’t) doing through the assessment process.
What considerations are made when integrating a DAS at your facility?
A DAS is your compliance engine, period. Calculations and data validation should be completed in the DAS and sent to other “systems” at your facility. Compliance averages should never be calculated in more than one (1) place! This will only lead to discrepancies and related issues as existing regulations are clarified or new ones added. Not to mention that these “other” systems were most likely not designed to valid and calculate averages consistent with the regulatory requirements. Your resources are better spent validating one (1) robust compliance engine and using that tool to push the results to “other” systems such as Distributed Control Systems (DCS), PI Historians, or Environmental Management Systems (EMS). Please note that fitting a DAS into your current data management system could have complications and must be considered as part of the DAS implementation process. For example:
- What other parameters do you need to express in terms of the emissions standard?
- How do you assign unit operational status?
- Where do the data come from?
- Where does it need to go?
- Are the associated connecting “systems” compatible?
What will your future DAS needs include?
One (1) guarantee is that your future monitoring needs will only increase and that reporting will continue to become more electronic in nature requiring the DAS to generate specific-types (i.e., .xml) for direct upload to the regulatory agencies [e.g., U.S. EPA’s Electronic Reporting Tool (ERT), etc.]. How will your DAS (and vendor) track and anticipate these future needs? How can future sources, monitoring parameters, and reports be added to the DAS? You will need to ensure that a new or upgraded DAS will be able to provide future compliance solutions. You will need to challenge your DAS vendor on what their future concerns are, how they are tracking and addressing an evolving regulatory and monitoring climate, and most importantly how your vendor will keep you apprised of and compliant with upcoming changes.
What type of DAS do you need?
At first glance, your DAS needs can be dictated by what regulations you are required to demonstrate compliance with. Nowadays, DAS are effective tools that do far more than just calculate and validate compliance averages. Your DAS can also be used to manage routine (but tedious) quality assurance and related activities (e.g., cylinder gas audits, linearity checks, relative accuracy test audits, manage calibration gases, generate regulatory specific reports). DAS vendors are constantly adding “bells and whistles” to set their product apart to provide a tool that can also increase productivity. Whether it is a CMS downtime or excess emission event, the DAS must also have notification capabilities. It is not uncommon for a DAS to generate alarms that are transmitted via email or text notifying the proper parties of an event. While it is great that the notification capabilities of a DAS can trigger responses from the appropriate facility personnel, the actions taken may be reliant on other systems at the facility.
What other resources do I need when implementing a DAS?
The implementation of a DAS can have a domino effect on other systems at your facility. In the long run the identification of weaknesses in supporting systems will result in an overall stronger compliance solution. However, if the transition is not appropriately planned for, the fallout can be overwhelming. Sometimes, weaknesses in supporting systems can cause the implementation of a DAS to slow down or stop all together while these systems are addressed. In other cases, the Environmental Department may manually fill in the gaps, thereby preventing the final delegation on certain activities. For example, the DAS provides the means for data quality responsibilities to be delegated to the Instrumentation Department. Imagine that a DAS notifies the Instrumentation Technicians that a CMS is not generating quality assured data. The Instrument Technician springs into action, repairs the CMS, and returns it to service. What’s next? Do any additional quality assurance activities (i.e., calibration, cylinder gas audit) need to be completed? What does the CMS Quality Control/Quality Assurance (QA/QC) Plan require, if anything? Do you even have a QA/QC Plan, or a site-specific monitoring plan for a MACT standard? The point is that the QA/QC Program will most likely need to be revised to complement the DAS platform.
After the Instrument Technician completes all of the required activities, he/she now acknowledges the alarm triggered by the DAS in order for the CMS downtime report(s) to be completed “real-time” as the events happen (or shortly thereafter once the issue is resolved). How does the technician know how to categorize the event when acknowledging the alarm in the DAS? How was the technician trained? Typically, additional training will also be required for all parties, including Instrumentation Technicians, to get the most out of your DAS. At the end, when all the systems fit together your DAS will become an asset to your compliance solution.
Even though we only highlighted a few questions to consider, there are many more aspects to identify and work through when fully implementing a DAS. Remember that implementing a DAS is a major commitment of facility resources that will extend (and if properly implemented will provide benefits) beyond the Environmental Department. The effort to implement a DAS will also extend far beyond the hardware and software pieces and challenge “other” systems that may be already fully functional. However, once fully implemented it can provide a compliance tool that can minimize your regulatory exposure while saving time. Understanding the entire process, and anticipating the issues that will arise, allows for a more successful implementation of a DAS. For more information on the process by which DAS are implemented, please feel free to call at 610.933.5246 ext. 117 or email me at eswisher@all4inc.com.
“