How Will You Be Determining Your Clinker Production Rate In Order to Demonstrate Compliance With the PC MACT?
Posted: April 15th, 2015
Authors: JP K.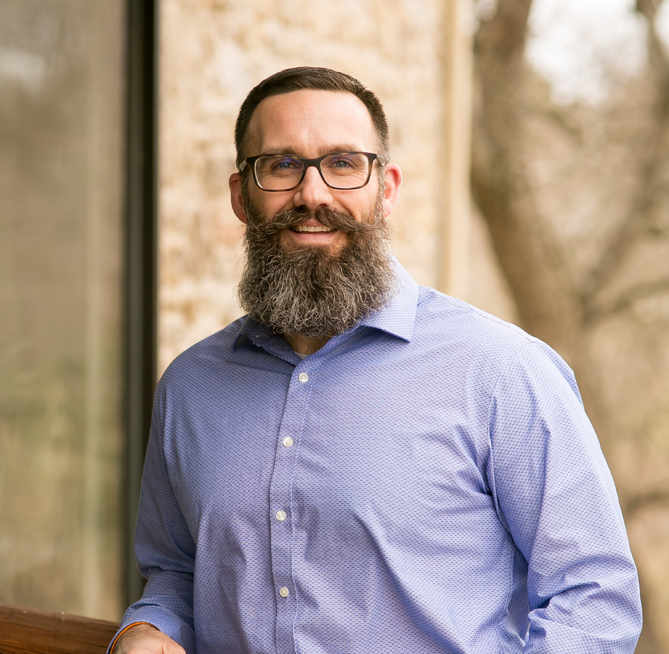
This blog post focuses on the clinker production monitoring requirements for PC MACT and presents questions that you should consider when developing your compliance strategy.
Before I outline the specific clinker production monitoring requirements, let’s take a moment to revisit why affected facilities need to determine their clinker production rate. A few PC MACT emission limits, such as particulate matter (PM) and mercury (Hg), are in units of pounds of pollutant per mass of clinker produced [i.e., lb/ton clinker or lb/million (MM) tons clinker]. Also, let’s not forget to include the emission limits that don’t appear in “Table 1” of the rule. Specifically, if your operations combine the clinker cooler exhaust or coal mill exhaust with the kiln exhaust, you may meet an alternative PM emissions limit that includes a 1.65 ton feed per ton clinker conversion factor. Therefore, monitoring clinker production is required to demonstrate compliance with these specific emission limitations.
You are probably thinking that we already have an established process for determining clinker production rate, which we have been using for years, and I’m not reinventing the wheel. So what’s the big deal? If you know me, you know I would tell you that “the devil is in the details.” Before I give you 99 reasons why you should be revisiting how you will be determining your clinker production rate for the PC MACT, let’s get clear on what the PC MACT clinker production monitoring requirements are, which are located at 40 CFR §63.1350(d) and also summarized below.
You must determine hourly (notice the emphasis on hourly) clinker production by one of two methods. Both methods require you to install, calibrate, maintain, and operate a permanent weigh scale system to measure and record weight rates in tons-mass per hour, which must be maintained within ±5 percent accuracy. The two options for a measuring system to determine clinker production are:
- The direct measurement of the amount of clinker produced, or
- The directed measurement of the amount of feed to the kiln and an applied kiln-specific feed to clinker ratio.
As noted above, measuring the amount of feed to the kiln requires an extra step to calculate your hourly clinker production rate. This extra step utilizes a kiln-specific feed to clinker ratio that is based upon reconciled clinker production and recorded feed rates.
That’s enough of the background; now it is time to get all tangled up with the details. I have identified below, in no particular order, a list of notes/comments/questions that hopefully spark your interest and get you into action now rather than later.
Feed to kiln method for determining clinker thoughts…
- Feed means the prepared and mixed materials, which include but are not limited to materials such as limestone, clay, shale, sand, iron ore, mill scale, cement kiln dust (CKD) and fly ash, which are fed to the kiln. Is your weigh scale system located in a position to record the weights of all feed materials? Do you insufflate CKD into the hot end of the kiln? Will your weigh system include this insufflated CKD? Does your weigh system need to include insufflated CKD?
- The PC MACT requires your calculated hourly clinker production to be based upon reconciled clinker production determined for accounting purposes. Do your clinker production records used for PC MACT compliance need to match your accounting records? Has this always been true—will it cause issues in the future? Furthermore, the PC MACT requires your clinker production ratio to be updated monthly. When have you historically updated this ratio—has it been monthly? Are your procedures for completing clinker production reconciliation documented?
- If your clinker production ratio changes at clinker reconciliation, you must use the new ratio going forward, but you do not have to retroactively change clinker production rates previously estimated. Will you retroactively change clinker production rates? That seems like more work? What if you have an emission limit exceedance and reconciliation will cause the exceedance to go away? Will you perform retroactive reconciliation on an as-needed basis? Do you remember Eric’s blog What should you be asking your DAHS vendor with respect to the PC MACT? How will your hourly clinker production rate be communicated and recorded within your DAHS? Will it be transmitted to the DAHS as an hourly value or will the system calculate the hourly values? Will a person need to manually input the data—when is the best time to do this? Can your DAHS accommodate retroactive clinker production reconciliation and reprocess the hourly emissions? What are the logistics for completing these processes?
- Remember that alternative PM emissions limit? It included a 1.65 ton feed per ton clinker conversion factor. Does this seemingly fixed factor get updated monthly? Does it fit into your reconciliation for accounting purposes?
Additional clinker production rate measurement thoughts…
- PC MACT requires you to determine, record, and maintain a record of the ongoing accuracy of the system of measuring hourly clinker production (or feed mass flow) each quarter of source operation. That doesn’t sound practicable. How do you plan to do this? Do you have the resources to do it in-house or will you need to contract a third party? Will you need to stop production to complete this requirement? If so, how long will it take? Are you going to include the procedure for the measurement system accuracy in your continuous monitoring system (CMS) Site-Specific Monitoring Plan?
- PC MACT requires you to measure clinker production directly, record the daily clinker production rates. Did you notice that the PC MACT requires you to determine hourly clinker production rates but, requires you to record daily clinker production rates? If you measure the kiln feed rates and calculate clinker production, you must record the hourly kiln feed and clinker production rates.
- PM emissions testing require you to determine a source specific 30-day rolling average operating limit using a lb/ton-clinker per milliamp value. This will set your operating limit at the PM CPMS output value. Mercury emissions testing requires you to calculate the emission rate using 30 days of clinker production during the same time period as the mercury emissions were measured. Again, how will retroactive reconciliation of clinker production affect your compliance with these testing requirements? How will your DAHS handle this?
You are probably thinking this is another PC MACT blog with lots of questions but not a lot of answers. That was intentional. The thought around developing a compliance solution comes now. If you have questions concerning this blog or any of the previous PC MACT series blog posts, give me a call at (610) 933-5246, extension 120 or send me an email at jkleinle@all4inc.com. I’d love to hear from you.