Demonstrating Compliance and the Importance of Permit Language (Sweat the Details)
Posted: February 28th, 2018
Authors: Roy R. Eric S. John E.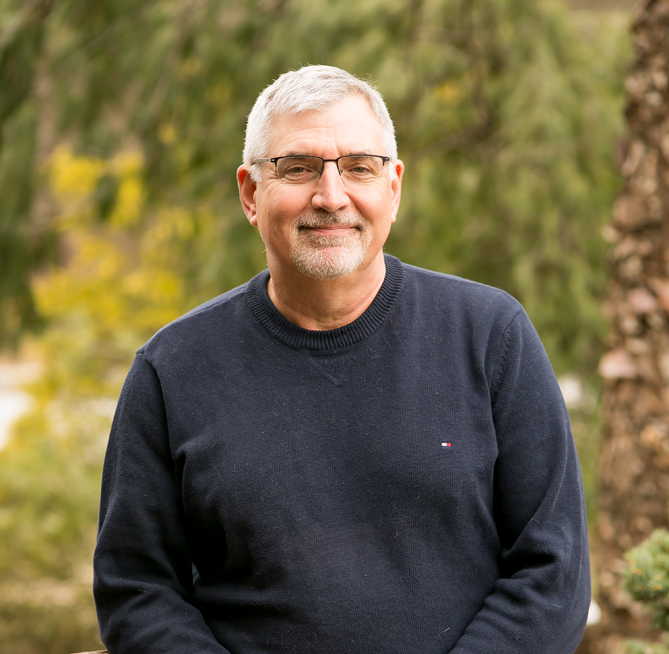
On the air quality side of the world of environmental compliance, ALL4 is seeing an increased emphasis on monitoring and recordkeeping, more specifically, electronic data and electronic reporting, as related to demonstrating compliance with permit requirements. Such data may be developed by continuous emissions monitoring systems (CEMS), continuous opacity monitoring systems (COMS), continuous parametric monitoring systems (CPMS), a “manually” observed record documented by a real person, or by documenting a work practice standard. One way or another, each little piece of data can take on a life of its own with potential negative repercussions as it makes its way into a compliance report or compliance certification, where it likely will be directly compared to a limit or standard, or become an important parameter used in a compliance calculation.
We have previously discussed the importance of all the of the systems, checks, and verifications that need to be considered and carefully assessed that can impact the validity of compliance related data. The use of CEMS, COMS, CPMS, data acquisition systems (DAS), and all the associated hardware, software, and “systems” that generate, compile, and report electronic compliance data have been discussed in multiple ALL4 blogs and 4 the Record e-newsletters. Equally important are the origins of the requirements to generate and collect the data in the first place and secondarily, the true derivation of the emissions limit or standard that the collected data are compared against to determine compliance.
How important are the associated requirements that specify how the collected data are developed, managed and reported? In most cases, the “keys” to the origin, interpretation, and derivations of requirements to generate, collect, quality assure, interpret, and report compliance related data can be found within the associated construction permit, operating permit or underlying regulation. When the origin of such limits and requirements are clearly spelled out in a Federal or state rule, there is an added level of clarity that instills a degree of confidence to the effort associated with generating and collecting data for reporting compliance. But what about limits and requirements that originate in air construction permits or that have been historically embedded in air operating permits where the origin isn’t so clear? In such cases, the permittee is left to complete the data puzzle by relying on habit, experience, guidance, and precedence. If regulatory “vague” limits and requirements in operating permits have not been revisited and carefully assessed, a facility could be in for some surprises, some good, some maybe not so good. Let’s consider a couple of relatively simple examples.
Example 1:
A facility is subject to an emission limit that is incorporated into their operating permit. The operating permit specifies an averaging period for compliance demonstration as “a 30-day rolling average”. Historically, the facility complied with the 30-day rolling average emission limit by simply calculating the average of the data collected over each 30-calendar day period. The origin of this permit condition was identified in a previous construction permit as 40 CFR Part 60 Subpart Db. In this instance, the original construction permit condition was not completely included in the operating permit. 40 CFR Part 60 Subpart Db specifies that compliance must be demonstrated on a “30-operating day average”. The key term “operating” was inadvertently omitted from the operating permit that incorporated the terms of the construction permit and was never caught by the facility or the regulatory agency. Compliance demonstrations that are based on a 30-day rolling average using “calendar days” rather than “operating days” will, understandably, be vastly different (during intermittent operations). In this instance, the facility is obligated to look past the literal language of the operating permit to fully understand the underlying requirements in the applicable standard to properly generate and report compliance data.
To expand on Example 1, some regulatory agencies will do you a favor by “streamlining” multiple permit conditions that, at first glance, may appear to be similar, even redundant. In many instances, permit language is written stating that compliance with one applicable standard or requirement assures compliance with other applicable standards or requirements, thereby “simplifying” permits and compliance demonstrations. While this concept works in certain instances, streamlining applicable standards or requirements can easily be mis-used by regulatory agencies. If emission standards were solely numerical, then streamlining conditions would be relatively easy and demonstrating compliance with a lower numerical limit specified in one standard would assure compliance with higher emission limits specified other standards. As we know full well, emission limitations are much more than just numerical values and include a suite of associated requirements including emission averaging periods, data validation requirements, definitions, and exclusions among other provisions. All the components of an emission limitation must be considered when permit conditions are streamlined. For example, consider data exclusions for periods of emissions unit startup or shutdown. Certain regulations may have specific provisions for startup or shutdown periods, while other rules may not even mention startup or shutdown. All things considered, even with permit streamlining, facilities are still obligated to demonstrate compliance with each individual applicable standard.
Example 2:
Like Example 1, a facility located in a state with state-specific CEMS regulations, is subject to an operating limit (i.e., minimum secondary combustion chamber temperature limit) that was established in accordance with 40 CFR Part §60, Subpart Ce and that is incorporated into their operating permit as a “3-hour rolling average”. With no further guidance or interpretation in the actual permit language, and because temperature data is measured continuously and recorded at 1-minute intervals, the facility conservatively interpreted the term “3-hour rolling average” to mean calculation of a new rolling 3-hour average every 180 minutes. Consequently, the facility repeatedly recorded and reported deviations of the minimum secondary combustion chamber temperature limit for the regulated unit. Upon further evaluation and research into the origin of the operating limit, it was determined that the continuous parametric monitoring system (CPMS) used to monitor compliance with the operating limit was not recording the data in accordance with the regulation. Consistent with the definition of one-hour period in 40 CFR Part §60.2, hourly averages should have been calculated on a “clock hour” basis. In this instance, the facility intended to report conservatively, which resulted in monitoring an operating parameter in a manner inconsistent with the regulation and resulting in the unnecessary and incorrect reporting of deviations to the state regulatory agency.
So, message one – make sure that the provisions in your air permit are clearly stated and include their basis and derivation, and specify associated provisions for emission averaging periods, data validation requirements, definitions, and exclusions. They need to be accurate and leave no room for ambiguity or misinterpretation. This leads to the second important consideration; message two – when you are in the process of obtaining a construction permit, the opportunity exists to ensure that requirements for monitoring and reporting compliance are grounded in applicable requirements and leave no room for misinterpretation.
If you’ve been at this a while you’ve seen how the air construction permitting process can get tangled in technicalities. If you are new to this, it is something you will very quickly learn. Regulated facilities are most often under pressure to obtain a construction permit as quickly as possible and may not have the final technical project details commensurate with air permitting timelines. Project specifications are prone to change during the permit review period. Standards and limits can also change during the process, as can the underlying rules themselves or agency guidance or interpretations. Anything is possible from the time the environmental team starts the air permitting process until the time the air permit is issued.
The greater the level of pressure imposed on the air permitting team – and by team, I mean everybody involved including facility engineering and environmental staff, facility operations staff, management, consultants, and agency staff – the greater the chance that uninformed decisions will influence the final permit. The unintentional result may be that the permit specifies limits and compliance requirements that are difficult or problematic to comply with, as evidenced by the previous examples.
What does this tell us? In the heat of the moment you cannot just agree to requirements where the actual process for demonstrating compliance has not been carefully vetted and laid out in clear detail. Failure to consider this can lead to overly complicated requirements for determining and demonstrating compliance, requiring extra time and manpower, and potentially setting up the facility for failure (i.e., non-compliance). Don’t let the pressure to get that permit as soon as possible be the cause of potential compliance issues once you are up and running.
In closing, please keep the following in mind related to air permits, emissions limits, and compliance monitoring:
- Ensure that construction permit applications properly cite and characterize emissions limits to include the appropriate numerical value(s) and all associated monitoring, recordkeeping, and reporting requirements and conventions.
- Fully understand the bases of numerical and parametric operating permit limits and ensure that the operating permit specifies all the provisions that comprise the standards. In the same vein, ensure that the required CEMS, CPMS, and related systems used to demonstrate compliance comport with all the components of the standards.
- Beware of “streamlined” conditions where a permit condition is structured in a manner where compliance with one numerical limit assures compliance with another numerical limit for the same pollutant.
- Resist the temptation to compromise on permit conditions in a construction permit in exchange for a promise of an expedited issuance of said permit.
ALL4 regularly assists our clients with all aspects of air permitting and compliance. We can support you with planning new projects to ensure that permit conditions are properly established, provide resources to audit your existing compliance tracking and reporting, and help you fix situations were historic reporting issues might be identified. Please reach out to Roy Rakiewicz at rrakiewicz@all4inc.com or Eric Swisher at eswisher@all4inc.com if you have any question on the topics discussed here, or if you would like to talk about any upcoming projects at your facility.