Cleaner Air Oregon, Four Key Takeaways
Posted: May 4th, 2020
Authors: All4 Staff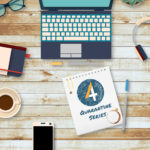
“As a cancer survivor, I must ask for much stronger protections in the Cleaner Air Oregon plan. As currently written, it does little to bring down cancer risk.”
- Public Comment provided during the October 2017 – January 2018 Oregon Department of Environmental Quality (ORDEQ) Comment Period
In April 2016, Governor Kate Brown launched the Cleaner Air Oregon (CAO) rulemaking process after communities raised concerns about exposure to potentially harmful heavy metals and chemicals emitted as pollutants from factories and other industrial sources. This program, which targeted a list of “Toxic Air Contaminants” (TAC), was a complete regulatory overhaul and was adopted by Oregon in November 2018 to close perceived regulatory gaps that remained in the various Federal programs to control air toxics. It has now been over a year since these rules have been put into effect, so how have they begun to impact businesses?
- Existing facilities have been prioritized and are slowly being “called in”
Any existing, permitted facility should be aware that ORDEQ has given them a prioritization score, placed them into one of four priority groups, and has begun to “call-in” Group 1 facilities. Once a facility is called-in, a regulatory clock starts ticking on a number of CAO requirements. The facility will be required to complete an analysis (Level 1, 2, 3 or 4 Risk Assessment) based upon the permitted emissions sources to evaluate their air toxics emissions. The level of analysis used impacts the complexity of analysis, associated costs, and timeline for compliance. Additionally, as part of the CAO process, each facility has a dedicated web page on ORDEQ’s website detailing the facility’s purpose, address, air permits, and assessment status.
Since beginning the call-in process, eight facilities (two in each ORDEQ Region) have been asked to start the CAO process which begins with the submittal of a TAC emissions inventory. Of these eight facilities, six facilities are in the process of completing the air toxics analysis, and two have met and completed the CAO evaluation. The two facilities that have completed the CAO evaluation met Level 1 Risk Assessment requirements, so they were not required to complete air dispersion modeling. This sped up CAO’s approval and made the call-in process for these facilities straightforward. For an existing facility, this should raise concern, however, because it is expected that most facilities in Group 1 and Group 2 will to need to conduct a CAO Level 3 Risk Assessment, which involves the use of U.S. EPA’s recommended air dispersion model AERMOD. The other six facilities that are conducting Level 2 and 3 Risk Assessments are in various stages of submittal, but for many the process has taken up to a year. This delay in approval of the six larger facilities could signal future project delays, increased costs, and additional work. If your facility has never completed an AERMOD analysis, we recommend you get started ahead of your call-in.
- CAO requirements are still evolving
In the fall of 2019, an ALL4 client began the process of applying for an air permit for a new facility. Being a new facility, the company referred to the guidelines provided on the ORDEQ website and set up a pre-application meeting to discuss applicable permit requirements and forms. However, looking back, the meeting provided limited insight. Much of the guidance provided by the agency in the pre-application meeting shifted in subsequent discussions during application preparation due to changes in direction from CAO.
Will sources be required to submit the same documentation a year from now? It is unclear. New businesses need to understand that this program is still in its infancy and still taking shape, so they will likely need to work closely with the ORDEQ to meet changing conditions to obtain a new permit.
- CAO requirements are unique
CAO has unique requirements for determining source emissions. Unlike other state agencies which allow facilities to reference U.S. EPA AP-42 emissions document for Hazardous Air Pollutant (HAP) emissions factors, CAO provides facilities with TAC emissions factors from a combination of sources (e.g., South Coast Air Quality Management District, Ventura, National Council for Air and Stream Improvement) for a specific source category and fuel type. According to the agency, these are conservative factors that should be applicable to all equipment in the given emissions source category (e.g., diesel-fired internal combustion engines). However, these emissions factors don’t take into consideration unit size, manufacturer year, or other source specific factors. Facilities should be aware that they will be held to these given emissions factors and could be required to source test for TAC to show compliance.
Additionally, a unique CAO requirement compared to many other state agencies is the need for facilities to account for cold startup emissions in their air toxics analysis for internal combustion engines. The calculations required are extremely conservative and do not consider source specific factors unless a facility can support alternative numbers.
- Air Dispersion Modeling can get complicated fast
The CAO Level 1 Risk Assessment utilizes dispersion factors that are based on conservative worst-case screening air dispersion modeling results to estimate a worst-case scenario of possible risk. The only site-specific dispersion information that is utilized as part of the Level 1 Risk Assessment is the stack height (or area for fugitive sources) and distance to the property line. For the most part only facilities that have small emissions rates and stack heights and larger distances to property line (or at least 2 out of the 3) will be able to conduct a CAO Level 1 Risk Assessment.
A Level 2 Risk Assessment involves the use of AERMOD in screening mode (i.e., AERSCREEN). AERSCREEN incorporates use of site-specific stack characteristics, building information (to account for building downwash), terrain data, specific exposure locations, and site-specific land use parameters. However, AERSCREEN still relies on a screening meteorological dataset similar to the Level 1 Risk Assessment. Screening meteorological data is a worst-case matrix of all the meteorological conditions that could occur (and some combined conditions that almost never occur). The Level 3 Risk Assessment incorporates the use of AERMOD which is similar to AERSCREEN in every way except the use of actual meteorological data (usually collected at nearby airports). Since, AERMOD and AERSCREEN are so similar in their setup, ALL4 usually recommends skipping AERSCREEN and going straight to AERMOD which will produce fewer overly conservative results. A Level 4 Risk Analysis is an extremely comprehensive model that involves considering bioavailability of TACs and modifying exposure assumptions. Most facilities will not be required to complete the Level 4 Risk Analysis.
For those familiar with and who may have run SCREEN3 (the screening model to AERMOD’s predecessor ISC), AERSCREEN and AERMOD are more complicated and require the development of more input information necessary to run the more complicated dispersion calculations. What also gets complicated fast is the amount of data that is necessary to manage. On average facilities could be reporting anywhere from 10-50 TACs. Multiply that by the number of emissions sources, and then multiply it again by the number of exposure locations ORDEQ is requesting (typically 7,000 locations). Finally multiply your number again by 43,824 hours (the number of hours in the required 5-year meteorological dataset). Very quickly your CAO Risk Assessment includes over a million datapoints. Therefore, it’s not only necessary to have a trained air quality modeler involved, but you also need to be able to manage a large amount of data. This becomes increasingly important when you need to start analyzing the modeling results to determine what sources and what TAC may be driving risks and therefore require refinement. ALL4 has developed programming scripts specifically for managing the AERMOD results from a CAO Level 3 Risks Assessment.
If you’re interested in getting started on a preliminary CAO analysis before you’re called-in, looking to build or expand your next facility in Oregon, or have any questions about the process, please feel free to contact us. If you’re in Oregon already, don’t be surprised if you hear from us directly as we seek to communicate what we have learned so far, identify where facilities may need assistance, and to potentially “compare notes” with other facilities that have started the CAO process.